The Future of Metallurgy: Automated Machines Leading the Way
Metallurgy, the science and art of extracting and processing metals, has been a cornerstone of human progress for millennia. From the Iron Age to the Industrial Revolution, each leap forward has been driven by innovation in tools and techniques. Today, we stand at the cusp of another revolution—one led by automated machines. These advanced systems, blending robotics, artificial intelligence (AI), and real-time data analytics, are transforming every stage of metallurgical production, from ore extraction to finished product inspection. As demand for high-quality metals grows—fueled by industries like renewable energy, electric vehicles, and aerospace—automated machines are no longer optional but essential. They are redefining efficiency, safety, and sustainability, pointing the way to a future where metallurgy is smarter, faster, and more reliable than ever.
From Mine to Mill: Automating the Extraction Chain
The journey of a metal begins with extraction, and automated machines are revolutionizing how ores are mined and processed. Traditional mining relied on manual labor for tasks like drilling, blasting, and ore sorting—processes that are dangerous, slow, and prone to inefficiency. Today, autonomous drilling rigs, guided by 3D geological maps, can bore into rock with pinpoint accuracy, reducing waste and increasing ore recovery rates by up to 15%. These machines operate 24/7, unaffected by fatigue, and can reach depths or locations too hazardous for human workers.
Once ores are extracted, automated sorting machines take over. Equipped with sensors that detect chemical composition and density, these systems separate valuable ore from waste rock at speeds of 50+ tons per hour—far faster than manual sorting. In copper mines, for example, automated sorters have increased the purity of ore sent to mills by 20%, reducing the energy and water needed for subsequent processing. This efficiency ripples through the entire supply chain: less waste means lower transportation costs, fewer emissions, and higher yields.
At the mill, automated crushers and grinders, controlled by AI algorithms, adjust their speed and pressure based on ore hardness. This ensures that particles are ground to a uniform size—critical for efficient metal extraction in smelting. Unlike manual operators, who often set machines to a fixed speed, automated systems adapt in real time, cutting energy use by 10–15% while improving particle consistency. For large-scale operations, this translates to millions of dollars in annual savings.
Smelting and Refining: Precision at High Temperatures
Smelting, the process of melting ores to separate metals, is where automated machines truly shine. Traditional smelting furnaces required constant manual monitoring: workers would check temperatures, adjust fuel flow, and add fluxes based on experience, leading to inconsistencies in metal quality. A single miscalculation could result in impure metal, requiring costly reprocessing.
Today, automated machines in smelting facilities act as “digital smelters.” High-temperature sensors embedded in furnace walls continuously measure heat, while gas analyzers monitor emissions to ensure optimal chemical reactions. AI-driven controls adjust parameters—such as oxygen levels or carbon input—within milliseconds, maintaining conditions that maximize metal purity. In steel production, for instance, automated arc furnaces can hold temperatures within ±2°C of the target, a precision that reduces impurities like sulfur and phosphorus by 30%. This level of control is critical for producing high-strength steels used in bridges or wind turbine towers, where structural integrity is non-negotiable.
Refining, the final step in purifying metals, is also being transformed. Automated electrolysis cells, used to refine copper or aluminum, now self-regulate current and electrolyte concentration. This ensures that metals reach 99.99% purity, a standard required for electronics and aerospace components. In one aluminum refinery, automated refining systems reduced processing time by 25% while eliminating 90% of manual errors, resulting in a 10% increase in production capacity.
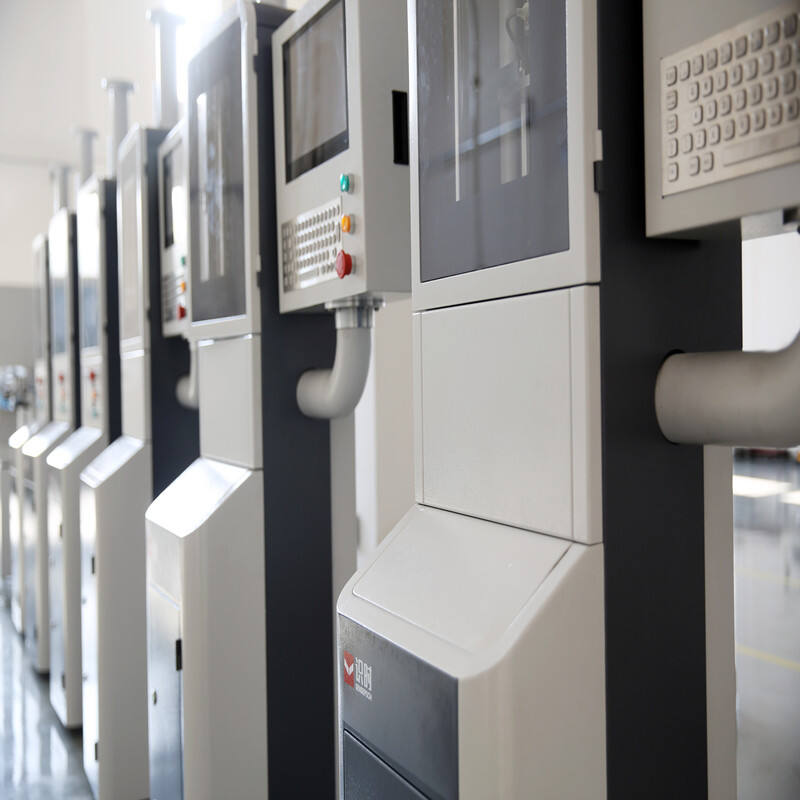
Smart Fabrication: Shaping Metals with Unprecedented Accuracy
Once metals are refined, automated machines take center stage in fabrication—shaping raw materials into finished products. Traditional metalworking, from forging to welding, relied on skilled craftsmen, but human limitations in speed and precision often constrained production. Today, robotic forging presses, guided by AI, can shape red-hot metal with forces exceeding 10,000 tons, ensuring uniform grain structure and mechanical properties. This is especially valuable for critical components like turbine blades, where even minor defects can lead to catastrophic failure.
Welding, a process historically prone to human error, is now dominated by automated machines. Laser-welding robots, equipped with vision systems, can join metal parts with seams as thin as 0.1mm, far more precise than manual welding. These systems detect gaps or misalignments in real time, adjusting their path to ensure a perfect bond. In automotive factories, automated welding lines produce 50% more parts per hour with 99.9% defect-free rates, a feat impossible to achieve manually.
Additive manufacturing, or 3D printing of metals, is another area where automated machines are breaking new ground. AI-powered 3D printers can build complex components—like heat exchangers or aerospace brackets—layer by layer, using metal powders. These machines optimize print paths to reduce material waste by up to 70% compared to traditional machining. What’s more, they can produce designs that are impossible with conventional methods, enabling lighter, stronger parts that drive innovation in industries like electric mobility.
Safety and Sustainability: Core Benefits of Automation
Automated machines are not just improving efficiency—they are making metallurgy safer and more sustainable. The industry has long been plagued by high accident rates, with workers exposed to risks like toxic fumes, heavy machinery, and extreme temperatures. Automated machines are taking over these high-risk tasks: robotic arms now handle molten metal in foundries, while drones inspect blast furnaces for cracks, eliminating the need for workers to enter hazardous environments. This shift has reduced workplace accidents by 60% in facilities with widespread automation, according to industry reports.
Sustainability is another key advantage. Automated machines optimize resource use: AI-controlled furnaces minimize energy consumption by adjusting heat output to match demand, while closed-loop water systems, managed by sensors, recycle 90% of water used in processing. In zinc smelters, for example, automated systems have cut water usage by 40% and reduced greenhouse gas emissions by 25% by precisely controlling fuel combustion.
Waste reduction is equally impactful. Automated sorting and processing ensure that more metal is recovered from ores, while 3D printing and precision machining minimize scrap. A steel plant using automated cutting robots, for instance, reduced offcuts by 35%, saving 2,000+ tons of metal annually. These gains are critical as the world moves toward a circular economy, where recycling and resource efficiency are paramount.
FAQ: Automated Machines in the Future of Metallurgy
Will automated machines replace human workers in metallurgy?
While automated machines handle repetitive or dangerous tasks, human workers remain essential for oversight, programming, and troubleshooting. The industry is shifting toward “human-machine collaboration,” with workers focusing on high-skill roles like AI system management and process optimization.
How do automated machines adapt to fluctuating ore quality?
AI algorithms in these machines learn from historical data, enabling them to adjust processing parameters (e.g., furnace temperature, grinding speed) when ore quality changes. This adaptability ensures consistent metal output regardless of input variability.
What role do digital twins play in automated metallurgical processes?
Digital twins—virtual replicas of physical machines or plants—allow operators to test changes (e.g., new smelting protocols) in a simulated environment before implementing them. This reduces downtime and risk, making automation more flexible and innovative.
Are automated machines affordable for small-scale metallurgical operations?
Yes. Many manufacturers offer modular systems that start with basic automation (e.g., automated sorting) and scale up as needed. Small plants often see ROI within 3–5 years through reduced waste and labor costs.
How secure are automated machines against cyber threats?
Modern systems include robust cybersecurity measures, such as encrypted data transmission and access controls. Regular software updates and employee training further protect against breaches, ensuring production continuity.
Table of Contents
- The Future of Metallurgy: Automated Machines Leading the Way
-
FAQ: Automated Machines in the Future of Metallurgy
- Will automated machines replace human workers in metallurgy?
- How do automated machines adapt to fluctuating ore quality?
- What role do digital twins play in automated metallurgical processes?
- Are automated machines affordable for small-scale metallurgical operations?
- How secure are automated machines against cyber threats?